The increasing demand for more specialized high quality steel grades as well as energy savings, drive the ongoing optimization of steel making processes. Steel making operations in general, and casting operations in specific, require good temperature control. In the steel making process, the quality of the steel is strongly influenced by the temperature of the liquid metal entering the continuous caster. Accidentally increasing or decreasing the steel temperature can result in poor steel quality, faster erosion of the refractory material and increased energy consumption and it can only be countered by performing real time tracking & monitoring of the ladles. Tracking of ladle position & it's retention time and monitoring ladle's as-is condition on real time basis are the major challenges for any large steel making operations. Currently, these operations are manually performed and logged into the system. The ladle position status is being exchanged through verbal communication using radio phones and the ladle monitoring is being done just on estimation. This practice reduces ladle circulation counts per shift per ladle and has bearing on important KPIs like safety, capacity utilization, resource utilization, time management etc
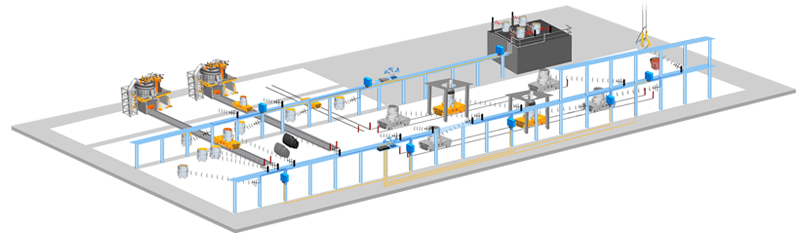
- Acquiring accurate timestamps for ladle arrivals and departures and accurate transit times, which are useful to track against SOP and helps to decrease ladle circulation time, crane logistics analysis and planning.
- Determining the exact contact time of each ladle which is used to evaluate the state of the refractory lining and other consumable parts.
- Calculating heat losses for waiting time, and correct temperatures for tapping and heating.
- The ladle monitoring system helps improve the safety of the operator and minimises the risk of damage to the plant by monitoring the ladle surface for hot spots and alerting operators before the condition becomes critical.
- The prevention of break-outs improves the safety of steel plant personnel. Break-outs occur when the refractory lining of a ladle excessively depleted in a particular area. The system detects the abnormal temperature increase caused by this depletion and generates an alarm signifying the need to remove the ladle from production and re-line it.