Many key tasks in the production environment like inspection, orientation, identification, and assembly, require the use of visual techniques. Nothing beats human vision for versatility, but human weaknesses limit productivity in a production environment. Visibility, eye estimation, manual instruction, boredom, distraction, fatigue, and sometimes even malice can degrade human performance. Totally integrated automation is the answer of all such human weaknesses. The USIT automation system is the first step toward better, faster, more flexible, intelligent and accurate production.
- Challenges
- Features
- Benefits
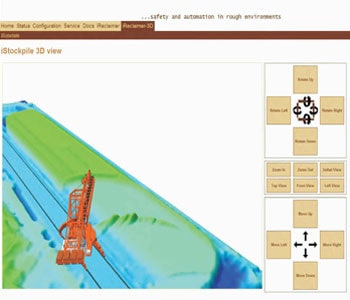
Automation
As per the work order generated by the operator sitting in the control room, the RMMS software calculates all the required positions like linear travel distance, slew and luff angle of boom as per the stacking or cutting instruction and sends instruction to the PLC. The machine automatically moves to the calculated starting position and handles the job as per the instruction.
iRRU is connected to the 2D Rader (used for stock profiling) and D-GPS(used for physical condition of the machine). The operation is continuously monitored and calculated by iRRU and the calculated data is sent parallel to PLC. As soon as it reaches to the desired results, PLC will trigger stop signal to bring operation to halt.
How an operator can realistically measure the distance to the face or cutting depth with his bare eyes? Is it 15m, is it 16m? this "tiny" difference has a big impact on the operation! Operators are forced drive by feeling, judging vibrations and waiting for slewing out of the pile. Get real-time and highly accurate information on cutting span depth, detect the bench edge height to automate stacker boom return movements, or make use of the many other monitoring options.
It Helps :
- Pile dressing as per the SOP and avoidance of moon surface.
- Increasing storage capacity and reclaiming performance
- Full utilization of equipment and stockyard
- Predefined stacking methods, such as Windrow, Chevron and Cone shell
- No over torque of machine means no overloading of conveyor belt
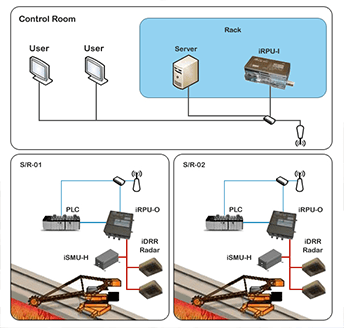
- 2D profile / 3D scanning for high accuracy.
- Insensitive to high environmental stress (dust, vibrations, wind, fog, snow, rain and thunderstorms).
- Constant update of the model at a measurement frequency of 15 Hertz.
- Industrial enclosure Ip66
- Contact-less measurement of luff & slew angle using D-GPS with precision accuracy.
- Safe and secure Man-less operation
- Exact inventory control
- Increased throughput
- Better utilization of the stockyard
- Improve stockyard visibility from arrival till dispatch
- Improve decision making Manage multiple stockyards with ease
- Smooth plant integration
- Minimal maintenance and cleaning
- Maximize operator efficiency
- Achieve accurate 2D / 3D snapshot of stockyard
- Real-time measurement during normal operation
- Operable under all environmental conditions
- 3D anti-collision system to avoid costly error
- Eliminate air reclaiming, ground digging, overloading / under-loading
- Full statistics and production history
- Optimal allocation of zone / section in stockyard
- Better stacking & reclaiming plan